MDF vs plywood: everything you need to know to choose
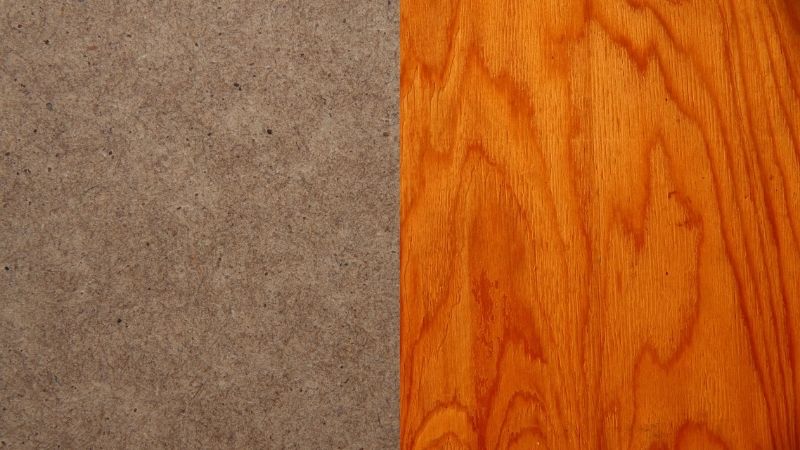
There is one activity that often takes more than 50% of my time every time I plan for a new project.
And that activity is answering this one question: what materials should I use for each component in my project? π€
More specifically, what primary, base material should I use?
While real wood is the strongest, best-looking base material to use, it’s often not the cheapest.
Besides, in many projects, the strength and beauty of real wood may be overkill.
For example, think of a vertical shelf for storing your toddler’s books and toys. Do you really need it to support 500lbs? Hopefully not. π
Two alternatives to real wood commonly used used are Medium-Density Fiberboard (MDF) and Plywood.
For a wide range of projects, including furniture, cabinets, shelves, and decorative accents such as wainscoting, MDF or plywood may be sufficient.
While that’s good to know, how do you go about choosing between MDF and plywood? What are the pros and cons of each of these materials?
The purpose of this post is to offer you a comprehensive comparison between these MDF and plywood.
Hope this post answers all the questions you have, and helps you choose between MDF and plywood for your project.
Enjoy!
1. Which is better, MDF or plywood? When to use MDF vs plywood?
Either may be better than the other depending on your project. While plywood is better than MDF in most applications, MDF may be a better choice for many projects.
The table below summarizes my findings of MDF vs. plywood. The sections that follow describe each of these table entries in detail.
MDF | Plywood | ||
1 | Stronger | β | |
2 | Cheaper | β | |
3 | Hold screws better | β | |
4 | Better for painting | β | |
5 | Better for staining | β | |
6 | More moisture resistance | β | |
7 | Better for outdoor use | β | |
8 | More durable | β | |
9 | Looks better | Tie | Tie |
10 | More versatile | β | |
11 | Safer to use | β | |
12 | Easier to work with | Tie | Tie |
13 | Environmentally friendlier | Tie | Tie |
14 | More fire resistant | Tie | Tie |
15 | More dimensional stability (less warping) | β | |
16 | Better for kitchen cabinet boxes | β | |
17 | Better for kitchen cabinet doors | β |
2. MDF vs. plywood manufacturing. How are they made?
MDF is manufactured by binding a mixture of wood fibers and glue into panels under heat and pressure. Plywood, on the other hand, is made by gluing together thin layers of wood (aka plies or veneer) peeled off logs.
The following sections describe these manufacturing processes in more detail.
2.1. What is MDF? How is MDF manufactured?
MDF (Medium-Density Fiberboard) is made by breaking down wood chips into wood fibers, combining it with a wax and resin binder, and forming panels by applying high temperature and pressure.
The infographic below illustrates the high-level steps in MDF manufacturing.
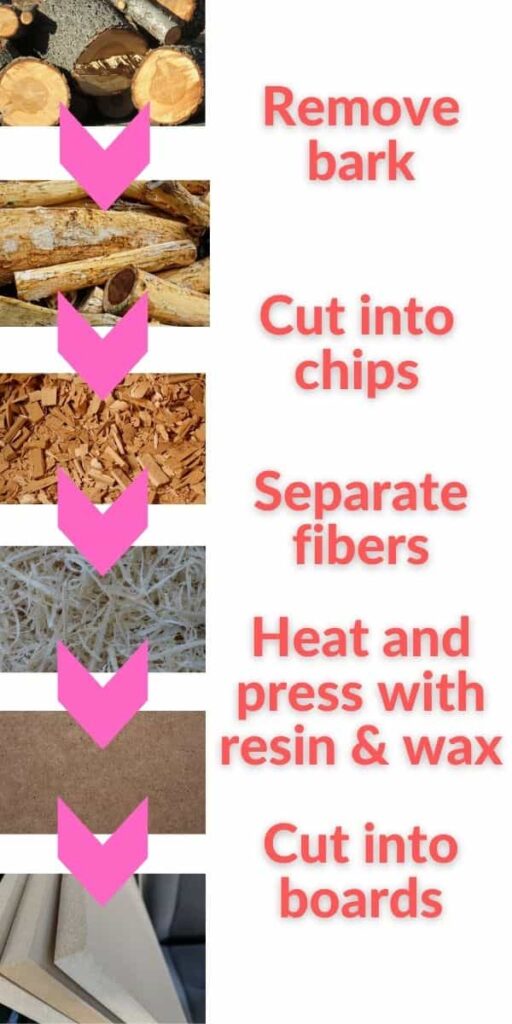
Following is a detailed description of each of these steps:
- Remove bark (debark): The first step is removing the bark from logged wood. In an industrial setting this is done semi-automatically as shown in this video, where high-speed, sharp-toothed grinding wheels scrape the bark off the log as it’s turned. Alternatively, jets of high-pressure water is used by some debarking systems. Note, MDF can be made from wood residuals, including scraps of lumber and recycled lumber, in which case this debarking step isn’t needed.
- Cut into chips: The debarked wood is then passed through a wood chipper to slice and dice the wood into small chips.
- Separate fibers (defibrate): The wood chips are then fed into a machine that shreds them into fibers. These wood fibers are the main component of MDF.
- Heat and press with resin & wax: The wood fibers are then mixed with resin and wax. The resin is the glue that binds the fibers together. Wax is added to help the fibers distribute evenly, and also to improve water resistance. The mixture is them rolled into sheets under high temperature and pressure. As per this source, MDF is typically made up of 82% wood fiber, 9% urea-formaldehyde resin glue, 8% water, and 1% paraffin wax.
- Cut into boards: The final step is to cut the MDF sheets into boards of desired sizes. The density of MDF is typically between 500 kg/m3(31 lb/ft3) and 1,000 kg/m3 (62 lb/ft3). This is generally denser than coniferous wood like spruce, pine, and fir, as per this chart.
Note: MDF can be made from wood residuals, including scraps of lumber and recycled lumber, in which case the first step above (debarking) isn’t needed.
2.2. What is plywood? How is plywood manufactured?
Plywood is manufactured by gluing together thin layers of wood peeled off logs under high temperature and pressure.
The infographic below illustrates the high-level steps in plywood manufacturing.
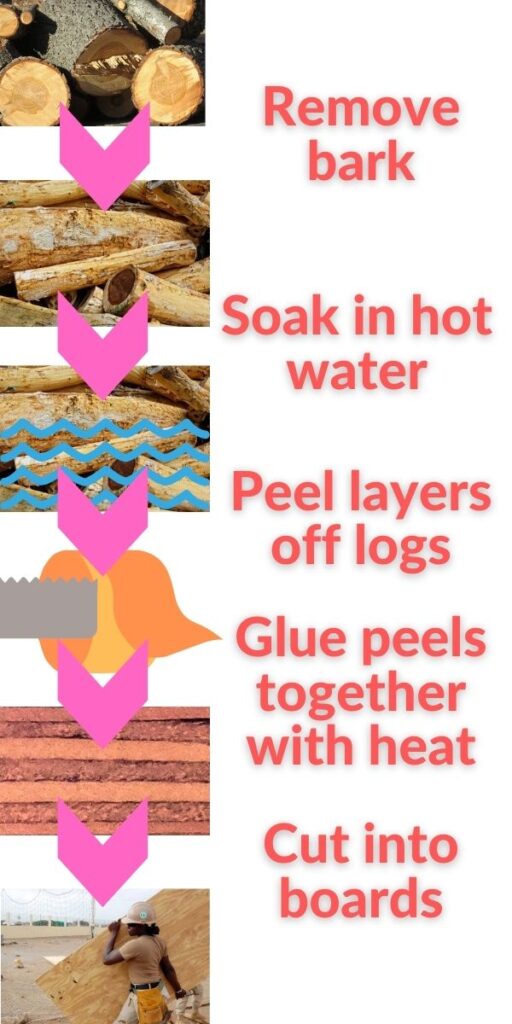
Following is a detailed description of each of these steps:
- Remove bark (debark): Similarly to the MDF manufacturing process, the first step is removing the bark from logged wood. In an industrial setting this is done semi-automatically as shown in this video, where high-speed, sharp-toothed grinding wheels scrape the bark off the log as it’s turned. Alternatively, jets of high-pressure water is used by some debarking systems.
- Soak in hot water: The debarked logs are then immersed in hot water to soften them. This step could take up to 2 days depending on factors such as the type of wood, and the diameter of the logs.
- Peel layers off the logs: The softened logs are then put on a lathe. As the lathe rotates a log rapidly about its long axis, a full-length knife blade peels a continuous sheet of veneer (ply) from the surface of the spinning log. A video illustrating this can be found here.
- Glue peels together under heat: Sheets of veneer are then stacked on top of each other with glue added between adjacent layers. Interestingly, adjacent veneer layers are rotated by 90o relative to one another such that their wood grains are perpendicular to each other. This is to add strength. The glued stacks are then pressed together under heat form a single sheet of plywood.
- Cut into boards: The final step is to cut the plywood sheets into boards of desired sizes.
3. What is stronger, MDF or plywood?
Plywood is stronger than MDF in general because the former is bound together by glue as well as layers of real wood veneer arranged perpendicular to each other. The latter on the other hand utilizes glue alone as the binding agent, to hold separated wood fibers together.
Plywood is also more flexible than MDF. You can gently bend plywood to create curves. Plywood’s flexibility (and shear strength) helps with stability when it’s used as sheathing in constructing residential or commercial buildings that can slightly shift or settle.
On the other hand, MDF tends to sag or split under pressure, like a soft cookie. βΉ In fact, long boards of MDF often sag under their own weight over time!
The weakness of MDF is most noticeable around corners and edges, which deform very easily, even if you press or scratch them gently with your finger nails! It was for this reason that I chose plywood for the corner shelves in my guest room with temporary walls project.
So, itβs important to reinforce MDF if youβre going to using it to build shelves or other weight-bearing furniture.
For example, some carpenters recommend no more than 28″ between vertical supports when building shelving with MDF. The bookshelf I have built with MDF sticks to this rule.
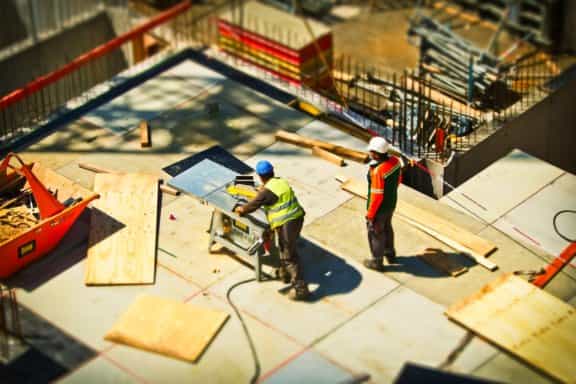
3.1. How strong is plywood exactly?
A 3/4″ thick, 12″ x 36″ piece of fir plywood can support up to 50lb without problems. One-inch thick plywood boards are strong enough to be used in concrete forms, stair risers, and industrial flooring.
The strength of plywood varies depending on 3 important factors:
- Thickness
- Wood species
- Number of veneer layers
3.2. How does thickness affect plywood strength?
Plywood’s strength increases with increase in thickness. For example, a 1/4″ thick, 12″ x 36″ piece of plywood will only support about 5lb before bending, whereas a 1″-thick plywood piece of the same size can support 50lb.
3.3. How does wood species affect plywood strength?
Plywood made from softwood, like those of conifer trees (pine, spruce, and fir) are weaker than those made from hardwood, like birch. This is because hardwood is stronger than softwood.
Even though hardwood plywood is in general much stronger than softwood plywood, the latter can be made stronger by using superior quality glue.
3.4. How does number of layers affect plywood strength?
The strength of plywood increases with increase in the number of layers of veneer.
A 3/4-inch-thick plywood containing 4 layers or less, the plywood has the minimum amount of strength.
A moderate strength plywood will have between 4 and 7 layers. It can be used for almost any project.
If the plywood has more than seven layers, it is the strongest. It can be used for special projects such as guitar bodies or router patterns.
4. MDF vs. plywood price. What is cheaper?
MDF is generally cheaper than plywood. One reason for this is that MDF can often be made from wood residuals, including recycled wood. Plywood, which contains intact wood veneers, often needs to be made from freshly cut trees.
The price difference between MDF and plywood can be very significant.
For example, the picture compares the prices of 4′ x 8′, 3/4″ thick MDF and plywood panels at Home Depot at the time of this post (February 2021).
Note: Plywood price can vary greatly depending on its quality or price. The higher the grade, the higher the price. The prices of some low-grade plywood can be comparable to those of MDF.
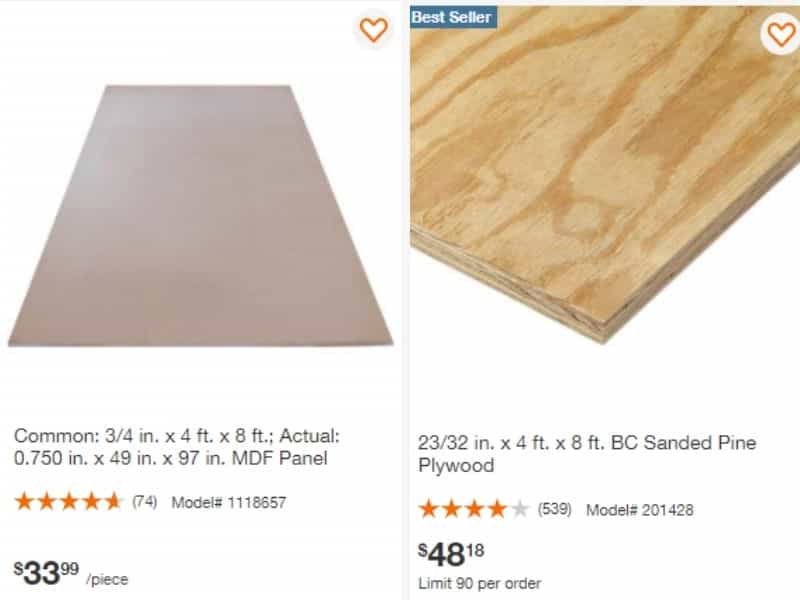
5. Which hold screws better, MDF or plywood?
Screws anchor better in plywood than they do in MDF, because of the wood veneers with grains embedded in plywood offer screws something to hold onto. In contrast, MDF has no grains, is softer, and therefore does not hold screws as tightly.
The inability of MDF to anchor screws well is particularly obvious near the edges, where MDF often splits if a screw is driven into its edges (parallel to the faces of the board).
Plywood on the other hand does not split like that.
This does not mean that screws cannot be used with MDF. They certainly can, especially for making furniture pieces like shelves that aren’t subject to a lot of stress or movement. You just have to be more careful with it.
I personally have used screws to join MDF pieces together, including in pocket joints.
If you’re using screws for MDF, be sure to use a coarse-thread screw. Most wood screws feature coarse thread.
6. MDF vs. plywood staining. Which is better for staining?
Plywood is substantially better for staining as its faces are made of real wood veneer with grains that stains can penetrate and highlight. While MDF can be stained, it soaks up stain like a sponge requiring several coats for the stain to be visible, and there are no wood grains for the stain to highlight making the effort not worth it aesthetically.
I actually stained MDF for one of my shelving projects, only because the project also involved real wood, which I wanted to stain, and I wanted to make the wood and MDF parts look similar.
Each MDF board in my project took 3-4 coats of stain before it started looking good.
With long brush strokes, I was even able to manage patterns that look like wood grain. See picture below.
But all those coats made for lots of work. π°
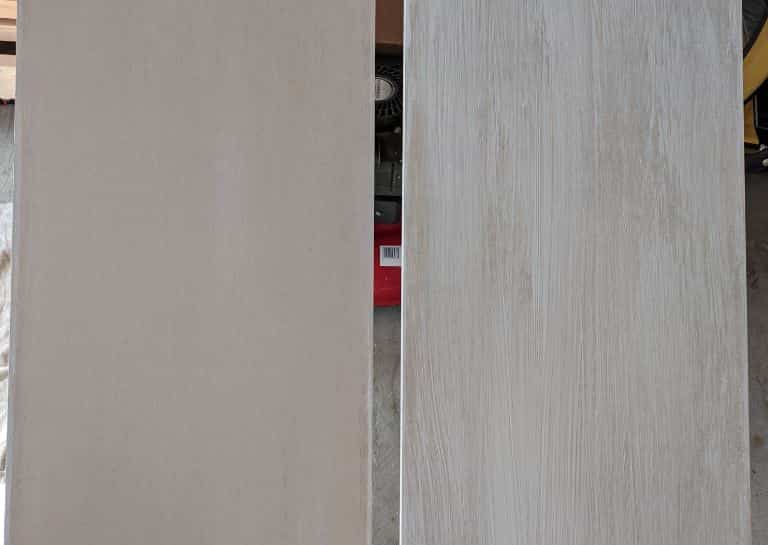
7. MDF vs. plywood painting. Which is better for painting?
Both MDF and plywood take paint well, but MDF, with its highly smooth surface, looks better when painted. MDF is often the better choice for upscale, painted applications such as cabinets and trim work as it’s easy to cut and free of the knots, rings, and wood grain.
A few tips to keep in mind when painting and finishing MDF:
- MDF comes from the factory sanded on it’s faces (the 2 sides of the board), typically with 180-grit smoothness. But the edges are still porous. It’s important for your project to either hide these edges. If you can’t hide the edges, seal them, e.g., with this drywall compound from Amazon, before painting.
- Prime the surface before painting, e.g., with this KILZ primer from Amazon for interior applications
- Avoid water-based primers and paints. MDF absorbs water like a sponge, resulting in the swelling of fibers on its surface.
Note: Priming and painting MDF makes it more resistant to water!
8. MDF vs. plywood moisture resistance. Which is more water resistant?
Plywood is more moisture resistant than MDF. However, neither are resistant to prolonged exposure to moisture, unless specifically made to be so.
The following subsections examine the moisture resistance of each material individually in more detail.
8.1. Moisture resistance of MDF
MDF boards that you typically see at home improvement stores are not moisture resistant. They’re for use in interior, low-moisture environments such as your home office.
When exposed to a high moisture environment like your bathroom, common MDF boards absorb moisture like a sponge, swell, and eventually disintegrate.
8.1.1. How to make MDF moisture resistant
The common MDF boards can be made more moisture-resistant by sealing them well, e.g., with thick coats of a primer and paint. See section above about painting MDF.
Sealed MDF boards can be used in high-moisture interior environments like your bathroom and kitchen. Note, common MDF won’t be ready for direct contact with water even after sealing, so you still wouldn’t want to use them outdoors!
8.1.2. Moisture Resistant MDF (MR MDF)
An alternative to buying common MDF and sealing it for moisture resistance is to buy moisture resistant (MR) MDF. MR MDF is like regular MDF, except that it’s made with moisture-repellent resin.
MR MDF is a bit more expensive than standard MDF
A green dye is typically added to MR MDF to make it easy to distinguish it from common MDF.
Similarly to sealed common MDF, MR MDF, though moisture resistant, is not water resistant. It’s not meant for direct contact with elements, and therefore cannot be used for outdoor applications!
8.1.3. Is there an MDF that can be used for outdoor applications?
Yes, there are multiple special MDF brands that can be used for exterior applications. These include Medite Tricoya Extreme Durable MDF and Greenpanel Exterior Grade MDF.
The former has been used in making garage doors and outdoor planters!
These exterior-grade MDF can withstand direct contact with the elements, including water and dirt!
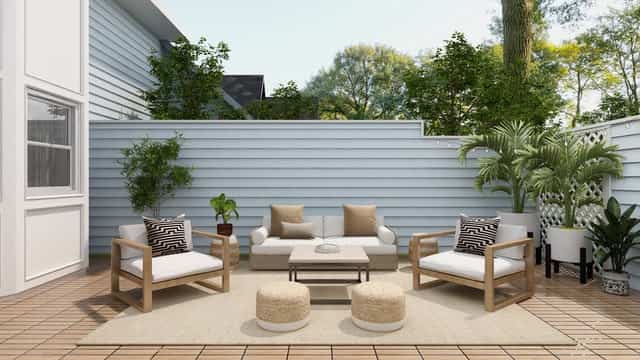
8.2. Moisture resistance of plywood
Plywood rated for interior use isn’t moisture resistant. But there are three other ratings of plywood, namely exposure 2, exposure 1, and exterior, each rating having higher moisture resistant than the previous one.
These plywood ratings are explained in more detail below.
- Interior plywood: This plywood is for use in low-moisture interior applications only, such as your home office
- Exposure 2 plywood: This plywood is made with a glue that is not fully waterproof. It can withstand occasional moisture but are otherwise intended for interior use.
- Exposure 1 plywood: This plywood has been waterproofed and can withstand exposure to the elements during construction. However, they are not suitable for long-term exposure post-construction.
- Exterior plywood: This plywood can withstand prolonged direct contact with water. It’s meant for outdoor applications, and is further categorized as follows.
- CDX plywood: This is the most common type of exterior plywood. This is what contractors typically use to build exterior walls and roofs.
- Marine grade plywood: This is similar to standard exterior-grade plywood, but its core consists of knot-free sheets, eliminating the possibility of the formation of water pockets within the structure. It’s typically used in the construction of boats.
- Pressure-treated plywood: This is interior plywood that has been infused with chemicals under pressure to give it added resistance to mold and mildew. Similarly to pressure-treated wood, the chemicals used are copper-based, which give this plywood a greenish hue and a slightly oily surface.
- T1-11 plywood. This plywood is designed for use as siding for buildings or cabins. It features a rough-sawn appearance that may or may not be grooved to simulate the appearance of vertical slats.
Note: Even if you use a plywood with an exterior rating for your outdoor application, it’s highly recommended that you seal it to extend its life. This sealing can be done with an epoxy sealer, paint, stain, or hard oil.
9. MDF vs. plywood exterior use. Which is better for outdoor applications?
Plywood is better for outdoor construction projects because there are many commonly available plywood ratings, including CDX, marine grade, T1-11, and CDX, intended for exterior use. In contrast, only a few, uncommon types of MDF, like the Tricoya Extreme Durable MDF, can be used outdoors.
10. MDF vs. plywood projects. What are the typical uses of MDF and plywood?
Both MDF and plywood are versatile materials in general, but commonly plywood has a lot more uses than MDF because of its advantages over MDF.
The table below lists some common projects or project types, and whether or not MDF or plywood is typically used for that project.
Note, you can make either MDF or plywood work for many of these projects.
Project | MDF | Plywood |
Interior furniture | β | β |
Cabinets and built-ins | β | β |
Shelves | β | β |
Flooring | β | β |
Decorative projects | β | β |
Speaker boxes | β | β |
Wainscoting | β | β |
Doors and frames | β | β |
Interior wall panels | β | β |
Roofing | β | β |
Outdoor projects | β | β |
Sheathing | β | β |
11. Which is more durable, MDF or plywood?
Plywood is in general more durable than MDF, given the former’s superior strength, resistance to moisture, and ability to hold screws better. At the same time, the durability of MDF may be sufficient for applications such as kitchen cabinet doors.
The durability of MDF is compromised particularly at the edges and corners, which get bent or dinged easily.
Another notable con of MDF is that scratches and dents on it cannot be repaired. The flaws will remain until you replace the board. In contrast these flaws in plywood can be repaired with sanding and refinishing.
12. MDF vs. plywood appearance. What looks better?
Either may look better than the other depending on the application. MDF looks better for architectural moulding involving complex cutting, e.g., with a router, as its lack of grain and orientation is conducive to cutting without chipping. On the other hand, plywood is better if you want your project stained or to look like real wood.
13. Which is safer, MDF or plywood?
But plywood is safer to work with and have around the house than MDF. MDF generates more, finer dust when cut, which can pose respiratory health risks. MDF also emits higher levels of urea-formaldehyde, a known carcinogen, to its surroundings.
13.1. Why does MDF pose health risks? What are the health risks of MDF?
The resin used to bind wood fibers together in MDF boards contains a chemical known as urea-formaldehyde (or urea-methanal formaldehyde), which MDF typically releases to its surroundings as gas. This is called off-gassing or outgassing, and it can be harmful to health.
Urea-formaldehyde is recognized as a Volatile organic compound (VOC) by the Environmental Protection Agency (EPA). A VOC is a compound of carbon (with some specific exclusions) which participates in atmospheric photochemical reactions.
A study from the Centers for Disease Control and Prevention found that high levels of this formaldehyde can irritate the skin, eyes, nose, and throat, and even lead to higher risks of cancer.
Additionally, when MDF is cut, sanded, shaped or machined in any way, it releases clouds of fine dust particles coated with formaldehyde. The particles, much smaller than those emitted by most other commonly used woods, can be inhaled deep into the lungs.
The picture below shows dust from cutting MDF in my garage workshop.
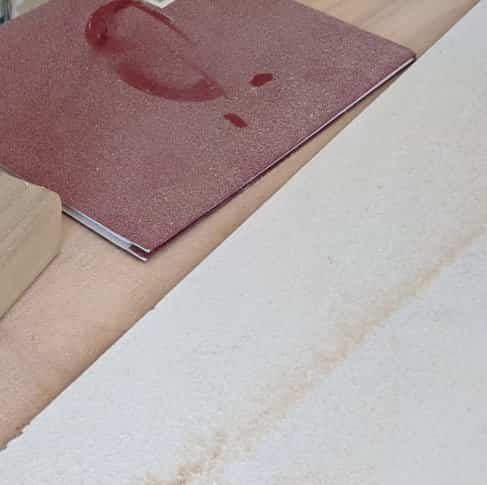
13.2. Why does plywood pose health risks? What are the health risks of plywood?
The glue used to bind wood veneers together in plywood can contain urea-formaldehyde, which plywood releases to its surroundings over time in the form of a gas. Similarly to MDF, this gas can be harmful to health. Plywood, like MDF, also releases formaldehyde-infused dust when it’s cut, posing respiratory health risks.
Still, plywood is safer than MDF, for multiple reasons:
- In general, the urea-formaldehyde levels of plywood are lower than those of MDF.
- Exterior grades of plywood are made with phenol-formaldehyde as the binder. Phenol-formaldehyde is less toxic than urea-formaldehyde as it off-gasses less. It also off-gasses faster, meaning most of the formaldehyde is gone by the time it gets to your house from the manufacturing site.
- In general, the finer the dust the more damage they can do to the lungs. Plywood dust particles are coarser, and therefore safer, than those of MDF.
13.3. What safety measures minimize the health risks posed by MDF or plywood?
Safety measures include wearing a mask and using a shop vacuum when cutting material, cutting in a well-ventilated area, letting the material air out outside the living space, sealing the material with a sealant like paint, storing the material in cooler temperatures, and buying material certified to have lower or no formaldehyde.
- Wear a mask and use a shop vacuum when cutting: Minimize the amount of dust by using a shop vacuum attached to the cutting tool. And, wear a protective mask.
- Use a well-ventilated area: Cut the material in a well-ventilated area, outside if feasible, to reduce the concentration of dust in the air around you.
- Let material air outside: Right after purchasing the material, let it air out outside your living space. The formaldehyde emission drops as days go by.
- Seal the material: Before installing, use a sealant like paint or oil to seal the material. This reduces the formaldehyde gas emissions.
- Keep your home cool: The higher the temperature, the higher the emissions. So, you slow the rate of emissions by keeping your home cooler.
- Buy certified material: Look for CARB II or NAF certified MDF or plywood. CARB II has lower emissions than non-certified material. NAF stands for No Added Formaldehyde, meaning a formaldehyde-free glue was used in making the material.
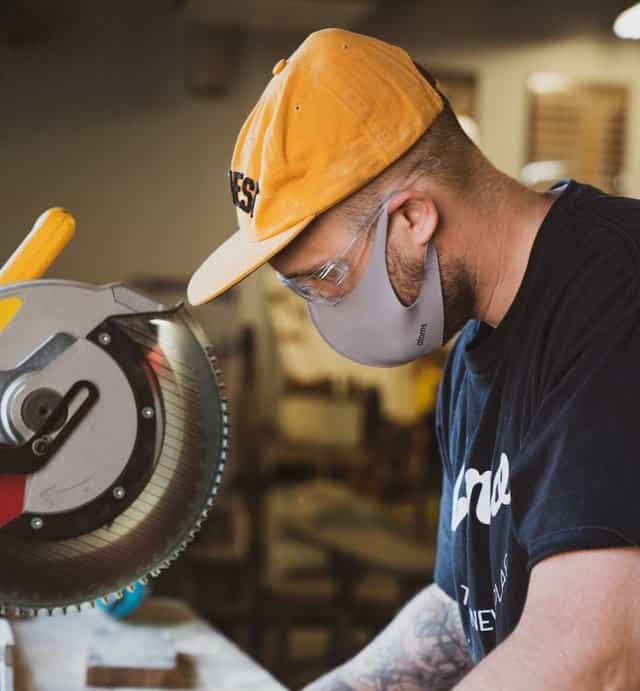
14. Which is easier to work with, MDF or plywood?
Either may be easier to work with then the other depending on the application. MDF is easier to paint, cut, drill, and machine. On the other hand, plywood is easier to stain, screw, build durable projects, and use in applications when moisture is a concern.
15. MDF vs plywood environmental impact. Which is more environment friendly?
The environmental impact of MDF is comparable to that of plywood. MDF often is made from recycled materials but is itself not a recyclable material. Plywood is often made from freshly cut trees, but is often recyclable into other wood-based products.
15.1. Is MDF made from recycled materials?
MDF can actually be considered a recycled product because it’s often manufactured using ingredients such as reclaimed wood chips from saw mills, plant fibers such as sugar cane fibers, waste paper, waste cardboard, and discarded phone books.
15.2. Can MDF be recycled?
Generally speaking, MDF cannot be recycled because of the high quantities of urea-formaldehyde often used to manufacture it. Urea-formaldehyde, a toxic substance and carcinogen, makes it difficult to recycle MDF into other materials.
Accordingly, some states, such as Tennessee, require fiberboard to be disposed of in a landfill.
Some studies, however, have shown that MDF-based mulch is safe to use for agricultural land. Still, recycling MDF isn’t common. Check with your local recycling operations to find out if MDF recycling is available in your area.
15.3. Is plywood made from recycled wood?
No, plywood is made of wood veneers peeled off fresh tree trunks, often cut down specifically for that purpose.
See my section above on plywood manufacturing for more details.
15.4. Can plywood be recycled?
Yes, plywood can often be recycled into other wood-based products as most of what plywood is made of is real wood. Check with your local recycling operations to find out if plywood recycling is available in your area.
16. Which is more fire resistant?
Neither plywood nor MDF is fire resistant unless specifically manufactured to be so. Fire resistant (FR) grades of both materials are available for purchase at home improvement stores.
FR plywood and MDF are often used in public building construction projects such as hospitals, schools, restaurants, and auditoriums for applications such as wall partitions, ceiling panels, and interior wall panels.
Regardless of where you purchase FR plywood or MDF, it is essential to look for the official stamp to ensure you are getting genuine fire-rated material that has passed the relevant tests.
17. MDF vs. plywood weight. Which is heavier, MDF or plywood?
A plywood board is lighter than an MDF board of the same dimensions, because MDF is denser than plywood.
Typical density of MDF is 600β800 kg/m3 or 0.022β0.029 lb/in3.
In contract plywood made from conifer trees have a density of 460-520 kg/m3.
18. MDF vs. plywood dimensional stability. What warps more, MDF or plywood?
MDF is less susceptible to warping under temperature and humidity variations than plywood because the wood fibers in MDF are oriented randomly. Plywood can warp, but the variations will need to be extreme for it to happen, because the wood grains of adjacent veneers in plywood are perpendicular to each other, minimizing warping.
The dimensional stability of MDF, i.e., it’s ability to expand and contract equally in all directions under temperature and humidity variations, is one of the biggest advantages of MDF.
This advantage sometimes makes MDF a better choice for components that are not fixed on all sides, like a door.
19. Which is better for kitchen cabinets, MDF or plywood?
Plywood, which is often referred to as “solid wood” by interior designers, is a better choice for making kitchen cabinet boxes. However, MDF is often a better choice for cabinet doors, even when the rest of the cabinet is made of plywood.
Kitchen cabinetry is arguably the most common use for plywood or MDF inside a home.
All things considered, plywood is the better choice for the box part (walls and shelves) kitchen cabinets because of its superior strength, durability, lighter weight, and moisture resistance.
When your interior designer says “solid wood” cabinets, they are often referring to plywood cabinets.
However, MDF is often the better choice for cabinet doors because:
- MDF is significantly cheaper than plywood. In fact, cabinet-grade plywood is one of the most expensive grades of plywood.
- Plywood is more susceptible to warping under extreme humidity and temperature variations.
- The smooth surface of MDF looks great when painted.
- Doors often require more intricate cutting and trimming, and MDF is more workable when machining or cutting.
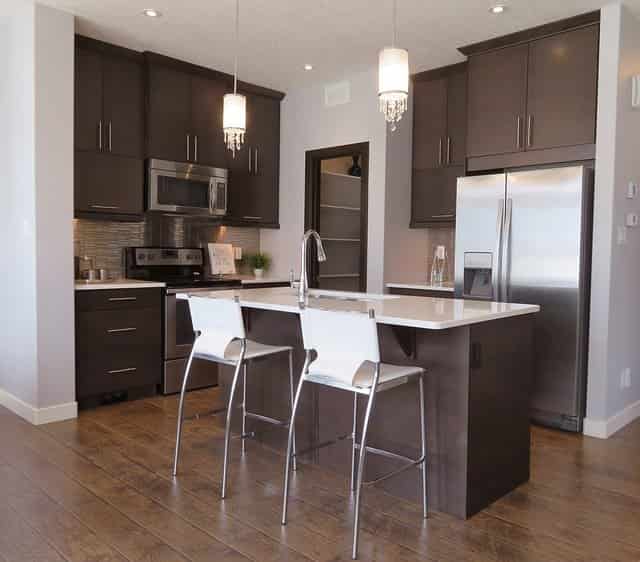